Common Mistakes in CNC Machining and How to Avoid Them
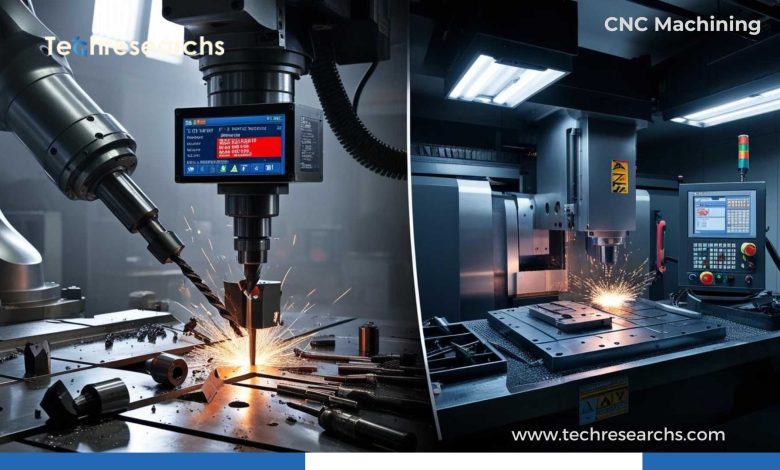
CNC machining is a highly precise and efficient manufacturing process used in various industries. However, even the most experienced machinists can make errors that lead to material waste, increased costs, and production delays. Understanding these CNC machining mistakes and implementing preventive measures can enhance efficiency and product quality. In this article, we will discuss common CNC machining errors and how to avoid them.
1. Poor Tool Selection
Choosing the wrong cutting tool affects the accuracy, efficiency, and longevity of CNC machines. A tool that is too large or small for the job can lead to uneven cuts and material waste.
How to Avoid It:
- Use tools designed for the specific material and operation.
- Regularly inspect and replace worn-out tools.
- Follow manufacturer recommendations for tool selection.
2. Incorrect Cutting Speeds and Feeds
Setting incorrect feed rates and cutting speeds can cause tool wear, overheating, and inaccurate cuts.
How to Avoid It:
- Refer to speed and feed charts for different materials.
- Use recommended speeds based on tool diameter and material hardness.
- Conduct test runs to fine-tune settings.
3. Improper Workpiece Clamping
Insufficient clamping can cause the workpiece to move during machining, leading to dimensional inaccuracies and safety hazards.
How to Avoid It:
- Use the correct clamps and fixtures for the material.
- Ensure the workpiece is securely held before starting operations.
- Regularly check clamps for wear or loosening.
4. Lack of Regular Machine Maintenance
CNC machines require consistent maintenance to ensure smooth operation. Skipping maintenance leads to breakdowns and inaccurate machining.
How to Avoid It:
- Follow a scheduled maintenance routine.
- Clean machines after use to prevent dust and debris buildup.
- Lubricate moving parts regularly.
5. Incorrect G-Code Programming
Errors in G-code can result in incorrect cutting paths, damaged tools, and scrapped parts.
How to Avoid It:
- Use simulation software to test G-code before running the machine.
- Double-check code for syntax errors.
- Train operators on CNC programming best practices.
6. Using Low-Quality Materials
Poor-quality materials can lead to machining difficulties, increased tool wear, and defective products.
How to Avoid It:
- Source materials from reputable suppliers.
- Inspect materials before machining.
- Choose materials suited for CNC processes.
7. Ignoring Tool Wear and Breakage
Worn-out tools cause poor surface finishes, dimensional inaccuracies, and machine damage.
How to Avoid It:
- Monitor tool wear regularly.
- Implement predictive maintenance strategies.
- Use coated tools to increase durability.
8. Lack of Operator Training
Untrained operators may struggle with programming, tool changes, and troubleshooting, leading to production issues.
How to Avoid It:
- Provide regular CNC machining training.
- Encourage skill development through hands-on practice.
- Keep operators updated with the latest machining technologies.
9. Not Checking Machine Calibration
Improper calibration results in inaccurate cuts and inconsistencies in production.
How to Avoid It:
- Regularly calibrate CNC machines.
- Verify settings before starting new projects.
- Use precision measuring tools to check dimensions.
10. Skipping Quality Control Checks
Overlooking quality control leads to defective parts and customer dissatisfaction.
How to Avoid It:
- Implement a strict quality control process.
- Inspect each part after machining.
- Use automated quality inspection tools when possible.
Table: Common CNC Machining Mistakes and Solutions
Mistake | Consequence | Solution |
---|---|---|
Poor Tool Selection | Uneven cuts, material waste | Use the right tool for the job |
Incorrect Cutting Speeds | Overheating, tool wear | Follow speed & feed guidelines |
Improper Clamping | Inaccurate cuts, safety hazards | Use proper clamps & fixtures |
Lack of Maintenance | Machine failure, low precision | Follow a maintenance schedule |
G-Code Errors | Tool damage, incorrect cuts | Simulate and review code |
Low-Quality Materials | Poor machining, increased tool wear | Use high-quality materials |
Tool Wear | Rough finishes, inaccuracy | Monitor and replace tools regularly |
Inadequate Training | Production errors, delays | Train operators regularly |
Poor Calibration | Dimensional inaccuracy | Calibrate machines frequently |
No Quality Checks | Defective products | Implement strict quality control |
Frequently Asked Questions (FAQs)
1. What is CNC machining?
CNC machining is a manufacturing process where computer-controlled machines shape materials into precise parts.
2. How do you prevent CNC tool wear?
Regular maintenance, using high-quality tools, and following proper cutting speeds help reduce tool wear.
3. Why is G-code accuracy important?
Accurate G-code ensures precise cutting paths, reducing material waste and tool damage.
4. How often should CNC machines be calibrated?
Calibration should be done periodically, depending on usage, to maintain accuracy.
5. What role does material quality play in CNC machining?
High-quality materials ensure smoother machining, less tool wear, and better end-product quality.
Avoiding common CNC machining mistakes requires attention to detail, proper training, and regular maintenance. By following these best practices, manufacturers can improve efficiency, reduce costs, and produce high-quality parts consistently. Implementing a proactive approach will ensure smooth CNC operations and long-term success.
More TechResearch’s Insights and News
Robotic Process Automation (RPA): Everything You Need to Know – TechResearchs